Many shades of orange
The diversity of our workforce is one of STIHL’s strengths. Every employee has the chance to make a difference, regardless of gender, origin, sexual identity, or disability. To underscore this mission, STIHL Brazil has launched its own diversity program.
STIHL is an employer. But it is also a member of society with a responsibility. That is why care is one of the focus areas of our sustainability strategy. Our commitment to diversity is part of it. “Treating each other with respect is one of STIHL’s core values, which is something we want to reflect in the image we project,” says Andréia de Borba de Souza from Human Resources at STIHL Brazil. Since 2019, the 37-year-old has been in charge of Programa Diversidade. The goal of the program is to foster diversity and inclusion among staff. “Diversity is the invitation to the party,” says Borba. “Inclusion is the invitation to dance.”
Both aspects contribute to a sustainable human resources policy under which everyone can leverage their strengths. The factors also play an important role in success, with studies indicating that diverse teams are often particularly innovative. The message to society is another factor. According to Borba, 56 percent of Brazilians are black, yet Afro-Brazilians only make up 4.7 percent of all business leaders. For women, those figures stand at 51 and 29 percent. STIHL Brazil aims to lead the charge for change, and has made both ethnicity and gender two pillars of its diversity program.
»Treating each other with respect is one of STIHL’s core values.«
HR Business Partner, STIHL Brazil
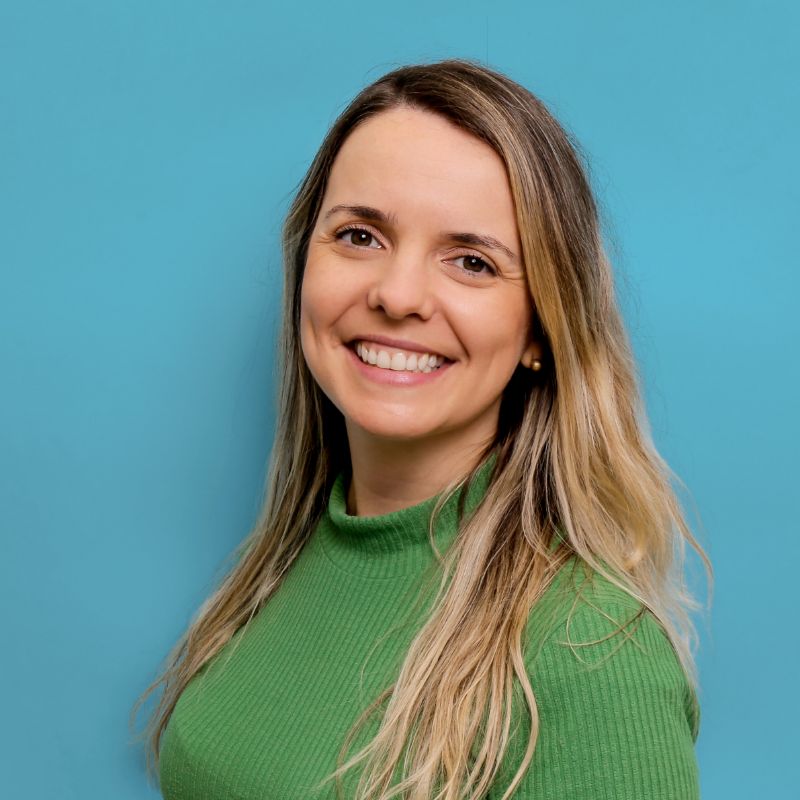
“We see a change in how people act”
Having started at management level, the program is now being felt on the factory floor. At its core, the strategy is about information and sensitization. New management staff complete mandatory “Diversity School” training. In group discussions, employees talk about ways to overcome prejudice and create acceptance for one another. International Women’s Day and Black Awareness Day, which commemorates the end of slavery, are celebrated together. Additionally, diversity and inclusion are constant elements of internal communication, advanced training, and recruiting.
The company does not use binding targets such as quotas, Borba explains. But success when it comes to soft factors is just as important. “We feel people’s pride, and we see a change in how they act,” she says. “It renews my motivation every day that we at STIHL are contributing to a shift in people’s mentality, and to a fair and respectful society.” For the fifth year of the program, she has her eyes set on a fifth aspect of diversity: “We’re thinking of setting up a working group on the topic of age.”
2019
Program founded at the STIHL Group company in São Leopoldo, now with 200 participants
“Programa diversidade” The diversity program at STIHL Brazil rests on the following four pillars:
Diversity
worldwide
Women’s networks
“Women Network @ STIHL” was launched at the STIHL founding company in 2023. Sponsored by Chief Financial Officer Ingrid Jägering, the network gives women an opportunity to connect, share experiences and best practices, and draw attention to their needs. Previously, the company had smaller networks, such as “Women in IT.”
Equal opportunity
Our Swiss chain plant focuses on equal opportunities during the recruiting process by looking at people and their abilities, regardless of factors such as gender, age, or origin. The same goes for career development, with opportunities for advancement open to all.
Women in management
At our subsidiary ZAMA in the Philippines, 70 percent of employees are women — as are 40 percent of management staff.
occupational-safety
We are dedicated to promoting and protecting the health of employees across the STIHL Group. We are constantly optimizing our approach to occupational safety and accident prevention while adapting our health management system to the needs of staff.
Organization and responsibilities
The plants at the German founding company, the STIHL Group production companies in Brazil and China, and ZAMA China have an ISO 45001-certified occupational health and safety management system, covering 64 percent of the entire workforce (previous year: 57 percent). The management system at the founding company was recertified in 2022, with the other countries successfully completing the process in 2023. In addition, internal and external audits are performed annually. Processes and directives regarding occupational health and safety are defined in our STIHL guidelines and standards. Overall responsibility for the topic lies with the STIHL AG Executive Board member for Human Resources and Legal Affairs. At our locations, dedicated specialists within the executive departments for occupational safety are responsible for compliance and the implementation of legal and internal guidelines. Safety officers in the departments also keep an eye on occupational safety and support their supervisors when it comes to implementing preventive measures.
Accident avoidance and prevention
The internal STIHL directives define a hazard analysis and risk assessment process for work involving machines and other activities, with the aim of systematically identifying risks at an early stage and avoiding potential hazards wherever possible. Hazard analysis is conducted jointly by the appointed management and safety officers. Occupational safety specialists provide guidance, training, and support during the process. Based on the findings of the analysis, we plan targets and measures to further increase occupational safety. New insights are incorporated right away into the safety instructions for our staff. We familiarize all external visitors and staff from outside companies with potential hazards, as well as the applicable safety measures and safety rules, before they enter any of the Group plants.
Accidents and incidents are reported to the local occupational health and safety departments. STIHL investigates such events in cooperation with the individuals affected and their supervisors. Whenever possible, the employee council is also consulted. In addition, we review the findings of the hazard analysis and make adjustments to it as necessary. Necessary measures resulting from the investigations are initiated immediately. Fields of action for further improvements are derived from the regular analysis of all reported incidents.
Workplace accidents
Our goal is to keep the number of workplace accidents as low as possible. The number of accidents at STIHL facilities involving STIHL employees, staff from outside companies, and visitors is included in our records. In 2023, the accident rate stood at 4.2 per 1 million hours worked and was therefore slightly lower than in 2022 (4.5). As in previous years, we recorded no fatal workplace accidents. In 2022, we launched a pilot project for Germany, Austria, and Switzerland that aims to reduce the number of accidents in the long term and further enhance our safety culture. Findings from previous accident analyses and inspections show that simple changes in behavior, such as avoiding the use of cell phones on stairs or storing materials properly in a way that keeps paths clear, can help prevent up to 80 percent of accidents. We invite employees to participate in these preventive measures aimed at increasing safety in the workplace.
With that in mind, we took a variety of measures in the reporting year, including the launch of the “Misch dich ein” (“Get involved”) occupational safety campaign. Through intranet articles, tutorial videos, and signs in various locations such as cafeterias and at the entrances to the factory floor, we aim to increase employee awareness of occupational safety even further. Constant exchange on safety issues among members of staff and with their supervisors is also important. That is why the topic is regularly discussed in team meetings as part of the “Ten minutes for safety” section. Unsafe conditions and potential improvements in each employee’s personal working environment are addressed openly, along with good occupational safety solutions already in place. The approach allows other departments to adopt ideas as needed.
Another aspect of the campaign involves strengthening the role of safety officers, who support supervisors in all departments when it comes to promoting safety. Visual reminders within the departments help make the safety officers better known among their colleagues, while regular meetings with occupational safety specialists ensure expert support and exchange. In addition, a cross-divisional workshop for all safety officers is planned for 2024.
Workplace accidents¹
2023 | 2022 | |
---|---|---|
Total workplace accidents | 145 | 187 |
Of which employees of STIHL Group companies | 127 | 150 |
Of which outside workers | 18 | 37 |
Serious workplace accidents (more than 6 months’ time lost) | 1 | 2 |
Of which employees of STIHL Group companies | 1 | 1 |
Of which outside workers | 0 | 1 |
¹ Includes workplace accidents with at least 1 day of time lost. |
Accident rate
(STIHL employees only) per 1 million hours worked
2023 | 2022 | |
---|---|---|
Total accident rate | 4.2 | 4.5 |
Serious accident rate (more than 6 months’ time lost) | 0.1 | 0.1 |
Training and communication
Occupational health and safety can only be ensured if all employees have the necessary awareness and have access to the necessary information. That is why companies within the STIHL Group provide all staff members with comprehensive training on a regular basis. They undergo a safety briefing at least once a year. Our continuing education program includes a wide range of learning opportunities such as fire drills and seminars on hazardous materials and load restraint. Employees who require special training to do their jobs, such as forklift or crane operators, receive the instruction they need. New managers and supervisors complete mandatory training on occupational safety. At the founding company, a total of 135 managers and supervisors took part in this two-day training program in the reporting year. In addition, we strengthen awareness among the workforce through constant communication by way of posters, written employee information, and regular contributions to the Executive Board report and the report of the management at company meetings. Employees can submit improvement recommendations related to safety aspects and other topics at any time using the local idea management system.
The STIHL plant in Qingdao, China, tested a new approach to fire prevention in the reporting year. Twenty-two teams from various departments received training on fire extinguishers, hydrants, and other equipment. Afterward, they had the opportunity to test their firefighting skills in a competition. The concept made it fun for staff to learn about an otherwise serious topic.
In the reporting year, STIHL Brazil demonstrated just how effective our awareness and training-based approach truly is. As part of a project to reduce the number of workplace accidents, 64 foremen and other members of staff spent a total of roughly 300 hours completing occupational safety training. Thanks to the training and other measures, this facility recorded a historically low occupational accident rate of 0.6 per 1 million hours worked – well below the upper threshold of 3.0. In 2023 alone, our colleagues in Brazil invested more than 5,800 hours on the job in fostering an even better safety culture and helped eliminate more than 3,200 potential risks.
Health management
We care about the health and satisfaction of employees. At nearly all production companies, the STIHL Group has company doctors or agreements with external physicians and occupational health experts who look after the occupational health needs of our staff and provide personalized medical support. STIHL also offers regular preventive occupational health exams and aptitude tests. At many locations, the Group even provides counseling and free annual flu shots.
Through a wide range of information and training offers, we promote the physical well-being and mental health of employees across the Group. We want employees to stay healthy, motivated, and able to perform in the long term and feel well cared for at STIHL. That is why we have developed classes on the four prevention principles of exercise, nutrition, addiction, and stress – even for our apprentices and student employees – and incorporated them into our training curriculum. The health management team provides a variety of options depending on the location, such as one-on-one physical therapy support, information on promoting good health, preventive measures, and sports programs. Consultation, training, and presentations on workplace ergonomics, nutrition, substance abuse, stress management, resilience, and mindfulness are also available. In 2023, the founding company spearheaded a campaign to help staff get into shape for the summer. Entitled “Fit für den Sommer,” the initiative gave employees an opportunity to prepare physically and mentally for the warm months ahead through cooking classes, exercise options such as circuit training, and seminars on topics such as healthy sleep. Health Day at our plant in Ludwigsburg centered on bicycle safety training, presentations on topics such as sleep and stress, core stability screening, and much more. The STIHL chain plant in Switzerland reached discount agreements with a variety of health and fitness service providers for employees, such as a gym. In 2023, the distribution center in Dieburg held resilience training as well as back pain prevention seminars.
Through our health-related offerings at STIHL, we are making a contribution to the goal “Good health and well-being” (United Nations Sustainable Development Goals, SDG 3), with a special focus on universal health coverage, access to vaccines, and the prevention of substance abuse.
Care program earns recognition
In the reporting year, the Brazilian Association of Human Resources recognized STIHL Brazil’s comprehensive Care Program with its Top Human Being Award. The program, which was launched in 2019, includes occupational health exams and vaccinations, services for pregnant and chronically ill people, information on nutrition and smoking cessation, and much more. In 2022, the São Leopoldo plant also dedicated its Comprehensive Health Care Center, which has three doctor’s offices, two dentist’s offices, a physical therapy space, and a lactation room. The center can be used by employees and their family members alike.