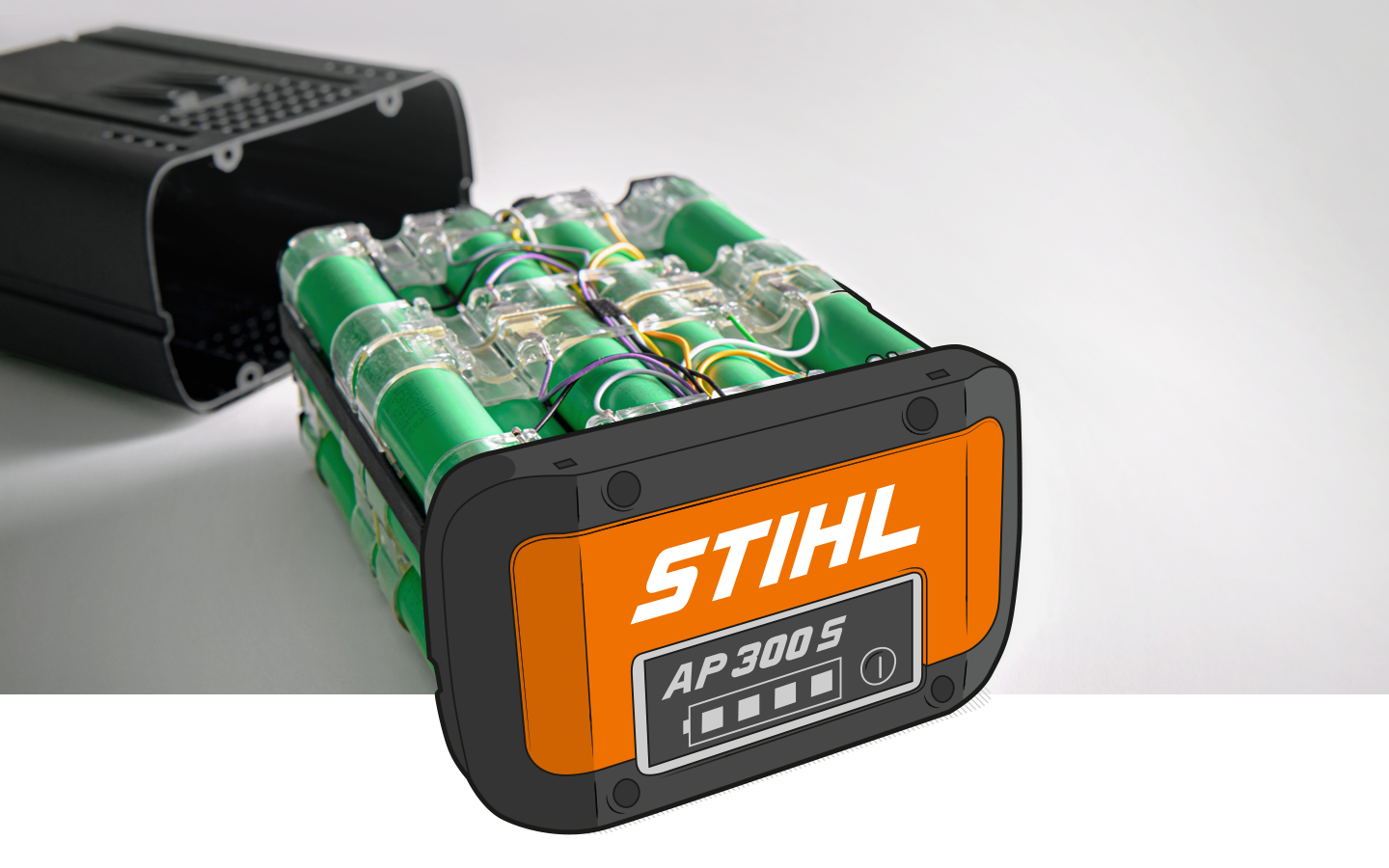
Vom Rohstoff
bis zum
Akku-Pack
Wo immer möglich, trägt STIHL Verantwortung für seine Lieferketten. Vor allem potenziell kritische Lieferketten versuchen wir transparenter und nachhaltiger zu gestalten.
Akku-Produkte sind leise, lokal emissionsfrei und werden immer beliebter. Vom Abbau der Rohstoffe über die Herstellung der Akkus bis hin zum Recycling sind die Prozesse jedoch an einigen Stellen intransparent und verbesserungswürdig. STIHL führt deshalb tiefergehende Untersuchungen bei potenziell risikobehafteten Lieferketten durch, um daraus Optimierungspotenziale abzuleiten und umzusetzen. Unsere Lieferketten der Mineralbeschaffung analysieren wir sukzessive mit Unterstützung der Responsible Minerals Initiative (RMI), der STIHL im Jahr 2021 beigetreten ist. Als Erstes haben wir die als besonders kritisch anzusehende Kobalt-Lieferkette unter die Lupe genommen.
Die Akku-Zelle
Zwar ist der Anteil von Kobalt in einer Lithium-Ionen-Akku-Zelle relativ gering, dennoch ist das Metall in leistungsfähigen Akkus derzeit kaum wegzudenken: Kobalt kommt als Basis für das Kathodenmaterial zum Einsatz. Es sorgt unter anderem für eine hohe Energiedichte der Zelle, lässt sie schneller laden und macht sie haltbarer. STIHL baut seine Akku-Zellen nicht selbst, sondern bezieht sie von einigen wenigen sorgfältig ausgewählten Lieferanten. Die enge Zusammenarbeit mit den Lieferanten und ständige Kontrollen gewährleisten die konstant hohe Qualität unserer Akkus.
Die Akku-Pack-Produktion
In einem Akku-Pack werden Akku-Zellen zu einem Paket zusammengeschaltet. Das Gehäuse hält die Zellen zusammen und schützt vor äußeren Einflüssen. Viele STIHL Akku-Packs stammen aus eigener Entwicklung und werden in Kooperation mit Lieferanten gefertigt. Die leistungsstarken Packs für professionelle Anwendungen produzieren wir auch in unserer eigenen Akku-Pack-Fertigung in Deutschland. In all unseren Akku-Packs sind ausschließlich Lithium-Ionen-Akku-Zellen verbaut, die sich in ihrer Mineralienzusammensetzung nur sehr geringfügig unterscheiden. Sie überzeugen durch hohe Lebensdauer und Energiedichte – bei gleichzeitig geringem Gewicht und geringer Selbstentladung. Zudem haben sie keinen sogenannten „Memory-Effekt“, das bedeutet, es gibt keinen Kapazitätsverlust bei einer Teilentladung.
Akku-Zellen
sind in einem STIHL AP 300 S verbaut.
Die Akku-Zellen-Fertigung
Für die Fertigung einer Akku-Zelle werden zunächst zwei Elektrodenfolien hergestellt – eine positive für die Kathode und eine negative für die Anode. Hierzu wird Kobalt gemeinsam mit den weiteren Mineralien und Additiven zu einer Paste verarbeitet, die hauchdünn auf eine mit Aluminium beschichtete Trägerfolie aufgetragen wird. Nach der Trocknung der Paste im Ofen wird die Folie aufgerollt, durch Walzen nachverdichtet und zugeschnitten. Danach folgt die sogenannte Assemblierung, der Zusammenbau der Akku-Zelle: mit einer Trennfolie, dem Separator, werden die Katoden- und Anodenfolien im Akku-Gehäuse im Wechsel aufeinandergestapelt, dann mit den Polen kontaktiert und ein Elektrolyt hinzugegeben. Nach dem erstmaligen Be- und Entladen folgt die Prüfung der Zelleigenschaften, das sogenannte Aging. Die meisten Fertigungsstätten für Akku-Zellen befinden sich in China. Zu den ländertypischen Risiken zählen hier lange Arbeitszeiten, geringe Löhne, mangelnde Sicherheit am Arbeitsplatz oder unzureichender Umweltschutz. Durch eine cloudbasierte Bewertungsplattform für Nachhaltigkeitskriterien erhöhen wir die Transparenz über unsere Akku-Zellen-Lieferanten und deren Produktionsstätten. Dadurch können wir gemeinsam mit den Lieferanten an Entwicklungspfaden für weitere Verbesserungen arbeiten.
Schmelze, Raffinerie & Vormaterial
Durch die Schmelze wird das Kobalt von Nickel, Kupfer und anderen Nebenprodukten getrennt und anschließend in der Raffinerie verfeinert. Die meisten Kobaltproduzenten befinden sich in China. Das reine Kobalt wird in festen Blöcken, als Platten oder Pulver bereitgestellt, welche die Basis für die weitere Verarbeitung bilden. Da die Vormaterialien in der Regel auf dem freien Markt gehandelt werden, ist eine weitere Rückverfolgung meist nicht möglich. Die Lieferkette ist hier noch sehr intransparent. Schmelzen und Raffinieren sind energieintensiv, sodass bei diesen Schritten von einem großen CO₂-Fußabdruck auszugehen ist. Chemische Abfälle, giftige freiwerdende Gase und Feinstaub führen oftmals zu Boden-, Wasser und Luftverschmutzungen.
Der Kobaltabbau
Kobalt wird überwiegend aus Kupfer- und Nickelerzen gewonnen. Mehr als die Hälfte des Kobaltvorkommens der Erde liegt im Südosten der Demokratischen Republik Kongo. Das Land hat sehr instabile politische Verhältnisse und nur rund 10 bis 20 Prozent der dortigen Minen werden legal betrieben. Diese sind vergleichsweise groß, arbeiten mechanisiert und liefern rund 80 bis 90 Prozent des abgebauten Kobalts im Land. Das übrige Kobalt wird von Kleinstbergbauern in illegalen Minen unter sehr schlechten, gefährlichen und anarchischen Arbeitsbedingungen gefördert. Für die Menschen vor Ort ist die Arbeit dort jedoch meist die einzige Möglichkeit, Geld zu verdienen. Umweltschäden, wie die Verseuchung des Wassers durch die Reinigung des Kobalts, wirken sich dort zusätzlich negativ auf die Gesundheit der Menschen aus.
Kobalt wurden 2021 weltweit gefördert. Die Karte unten zeigt die sechs größten Abbaugebiete.
Cobalt for Development
C4D arbeitet sowohl in Gemeinden als auch in Minenstandorten, da sie sich gegenseitig in vielen Aspekten beeinflussen. Die GIZ, die die technische Verantwortung für das Projekt trägt, arbeitet direkt mit den Minenarbeitern über lokale Kooperativen, Behörden und die Zivilgesellschaft. Letztlich arbeitet das Projekt an der Stärkung der Einhaltung der Gesetze, an der Verbesserung der Gesundheit und der Arbeitsbedingungen sowie am Umweltressourcenmanagement. Der flexible, modulare Ansatz des Projekts ist so konzipiert, dass er auf andere Bergbaustandorte und Gemeinden übertragen werden kann, verantwortungsvolle Bergbaupraktiken fördert und sicherstellt, dass der Kobaltabbau zur lokalen Entwicklung beiträgt.